The intelligence of the back-end tools will become the champion of the semiconductor manufacturing industry
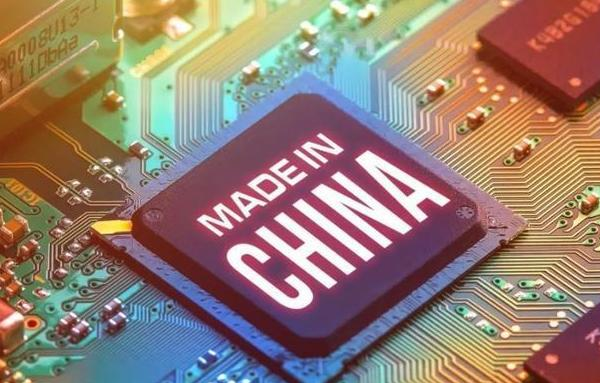
Becoming a semiconductor producer is a tricky process right now. In previously low-cost industrial areas, wages and energy prices have risen, while capital expenditures have climbed. At the same time, competition is heating up, with a slew of new businesses entering the market in recent years. Industry players are understandably anxious about these changes, and they have been pursuing a record amount of M&A activity in hopes of capitalizing on the next wave of productivity growth.
The manufacture of semiconductors is divided into two phases: the "front end" and the "back end." Back-end semiconductor manufacturing refers to the manufacturing operations after all circuits have been formed on the wafer. Revolutionary technology is created by combining extraordinary accuracy and precision with enormous throughput.
Servo drives are used in many operations in back-end semiconductor production because of their excellent performance and repeatability, which is what high-end semiconductor processing requires.
Most back-end factories in emerging countries have yet to use Industry 4.0 technologies in their critical operations, including wafer dicing, assembly, testing and packaging of individual semiconductors. Many of these factories are still struggling to implement the Lean methods common in front-end factories. Even when backend manufacturers reap some benefits from lean programs, they often struggle to keep up.
In the face of growing consumer demand and increased industry competitiveness, the relevance of back-end activities in semiconductor production continues to increase. More efficient tools are needed to assist with machine setup and batch scheduling decisions to achieve short cycle times, high throughput, and high utilization, while improving due date performance.
Ranking back-end tool process
Wafer Inspection
Optical wafer inspection looks for defects that could cause problems for the final product. Defects and annoyances as small as 30 nanometers can be detected, with effective uses as small as 10 nanometers. Electron beam inspection overcomes the limitations of optical inspection and is accurate to sub-3 nanometer resolution. Compared to optical inspection, e-beam inspection can identify the tiniest faults, but with lower throughput. As flaws and annoyances are discovered, they are mapped and corrected or avoided.
Wafer Test/Wafer Probe
The chips are first tested throughout the semiconductor manufacturing process to ensure they perform as expected. Functional checks are performed while the chip is still on the wafer, using a test fixture with pins to make contact with circuits on the surface of the chip. The chip's signal response is sent and measured by the probe. If feasible, repair faulty chips; otherwise, they are destroyed after the cutting process.
Dicing wafers
In this back-end semiconductor manufacturing process, the finished wafer is diced into individual chips. Mechanical sawing and laser cutting are two types of automation. The dicing saw uses a circular cutting blade to cut the die to a size of 35mm to 0.1mm for mechanical sawing. The chips are then transferred to the die bonding process using chip handling equipment.
Servo motion is used to align the dicing saw and wafer and adjust the dicing blade.
chip bonding
Individual chips are too small and fragile to handle individually. They must be protected and there must be an easy way to electrically connect to the chip. The process of bonding a bare die to a substrate is called die bonding or die attach.
In the next process, the substrate will serve as the interface between the tiny size of the chip and the large-scale electronic processing. It will also serve as the basis for the PC board protection chip package.
line connector
Wire bonding uses thin gold wires to connect each pad on the die to the corresponding pad on the substrate after die bonding. This connects the silicon chip inside the chip container to the pins on the outside through electrical connections. Wire bonding is used in traditional chip packages such as dual in-line packages (DIPs), which have the characteristic black oblong rectangle with silver pins protruding like bug legs, and PLCC packages, which have conductors on all four sides.
Wire bonders operate at breakneck speeds to maintain the large number of connections required for each chip. In fact, this is one of our most bandwidth-intensive applications.
Flip Chip / Solder Ball
Flip chips are mounted "backwards" as a modern alternative to wire bonding. As a result, the term "flip chip" was coined. Unlike the wires connected around the edge of the chip in wire bonding, an array of "bumps" is created on the surface of the chip. These bumps serve as connectors between the chip and the surrounding container. Here are some benefits of flip chip technology:
Better connections to chips, rather than wire bonds, add extra length, capacitance, and inductance, all of which slow down signal speeds.
Since the entire chip is exposed, not just the border, more connection sites are accessible.
Increase production speed
The overall package size is small.
package
When the back-end semiconductor manufacturing process is complete, the bonded chip and frame are sealed using a molding plastic compound or by attaching a sealing cover. Silicon chips are now ready for use in the electronics industry.
How to optimize backend tools?
Unlock the full potential of the workforce
Operator Contact Time Employees spend 30 to 50 percent of all work in back-end plants touching materials or running machines. Employees often sit idle for the rest of the workday while waiting for machines to complete their manufacturing cycles. Even if the production line is not running at full capacity, the ratio of employees to machines is consistent, which increases the duration of time that employees are not actively involved in the work.
Standard lean practices, such as changing worker-to-machine ratios based on operator contact time or employing flexible staffing to ensure that the number of people on the shop floor is sufficient for the plant's current capacity, have helped some back-end manufacturers improve labor productivity. These moves have yielded some benefits, but they are difficult to maintain, meaning back-end production remains labor-intensive.
Improve quality without delaying the production line
Engineering teams must study machine data and communicate with colleagues on the production line to identify specific production steps that cause losses in the event of production spikes or losses or unexpected quality issues at back-end facilities. However, engineers may only collect data once a week, making it harder to pinpoint the root cause long after the problem has arisen.
Engineers may need to interview line employees for information, and workers may recall some basic data about tool settings or other operating environments, which can cause delays.
Setting up dedicated yield and quality improvement teams and daily lean "meetings" may be a preferable approach. These organized discussions can help engineers grasp issues such as output stability and unpredictability so they can make improvements.
Consider throughput in a more proficient way
Most back-end factories rely on absolute metrics of uptime equipment available or unavailable, ignoring subtle results such as small downtime that don't result in a complete shutdown when evaluating OEE. Additionally, back-end manufacturers use manual procedures to track production losses, which only reveal broad patterns over time. These high-level conclusions do not give engineers a complete picture of what is causing production problems, making it difficult to develop strategies for improvement.
To address these issues, some return to lean fundamentals is required. For example, a manufacturer might form a continuous improvement team to prioritize and pinpoint the source of throughput bottlenecks. Many organizations have these teams, although they are not always present in the backend factory.
Consider a simple idea: Machines can be equipped with sensors to track major events that affect OEE, such as production failures or equipment failures. Operators will then enter contextual data through a touchscreen interface, saving time on manual data entry and providing engineers with a higher level of detail.
All in all, the semiconductor business is the leader in data collection; the problem is that companies only use some of the data they get. For the first time, advanced technology can help manufacturers tap into their vast knowledge base, providing the specific, practical insights needed to develop solutions.
Additionally, Industrial Revolution 4.0 tools automate many time-consuming processes that are now done manually in back-end factories. Together, these enhancements help managers execute lean initiatives faster and more efficiently, with some organizations seeing meaningful cost, throughput, and quality benefits within months.
Back-end factories that integrate smart manufacturing technologies may stand out in the competitive semiconductor industry, surpassing those with more traditional lean methods.